INTRODUCTION
With the current emphasis on biomass usage as a `green’ fuel for energy plants, it has become apparent that there is a need for understanding the requirements for storing biomass. Woody biomass, called `hog fuel’, has long been utilized as a fuel in cogeneration plants at pulp and paper mills, where it was traditionally a waste product from the processing of clean white wood chips used to make pulp. While many practical lessons have been learned about what is appropriate for hog fuel storage, generally little documented study has been directed at storage practices, primarily due to its abundance and historical status as a waste product with next to zero value.
However, hog fuel is the basic feedstock for biomass-fired power plants and is becoming a hot commodity and it is the single biggest on-going cost item for energy plants. How it is handled has an effect on quality, so a greater understanding of hog fuel storage requirements is required.
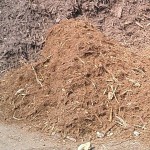
Biomass is not an easy material to handle. It appears in a myriad of species, forms and sizes; it knits together, doesn’t flow well, consolidates and packs easily; it can have a wide range of moisture contents, basic and bulk densities and calorific values. It will freeze; it is very dusty, catches fire easily and is self-combustible; it can contain all manner of contaminants.
What makes good hog fuel? When `greenfield’ plants are designed, boiler technology is usually selected based on the type of fuel available. When existing boilers are converted to burn biomass in `brownfield’ projects, the fuel must be matched to the existing boiler in order to minimize required boiler modifications. While individual fuel characteristics can vary considerably, there are four main fuel quality parameters that must be met to ensure good boiler operation, including maintaining:
- Consistent moisture content
- Consistent particle size
- Minimal contamination in order to minimize ash content
- Consistent calorific, proximate and ultimate values
1. Moisture Content of Fuel
Generally the dryer the fuel, the less energy is required to evaporate the remaining water and the more energy is available for generating heat or power. The amount of moisture contained in the incoming fuel has a great effect on the efficiency of the combustor, which is designed to operate best with a fuel that is maintained within a particular moisture band. Move outside that band and the boiler and/or its emissions control system is likely to have operating problems. For example, a boiler designed for fuel at 25% MC might have a burner efficiency approaching 80%; and if presented with fuel at 50% MC the burner efficiency could drop as low as 65%.
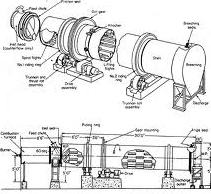
The most important requirement is that the moisture content is maintained as close to the ideal level for the particular boiler. Too dry fuel can cause as many operating problems as fuel that is too wet.
If your fuel is inherently wet, either the boiler must be designed to accommodate the wet fuel or the fuel must be dried prior to the boiler. In both cases, energy is required to drive-off the moisture, and finding the least costly way to do so can be a challenge. Drum dryers have been used to dry fuel before combustion, but in most cases that has proven uneconomical.
Bubbling fluidized bed boilers handle wet fuel the best, as the wet fuel is instantly dried in the sand bed just prior to combustion. All non-natural methods of drying the fuel require costly energy. However with enough space and time, wet fuel can be dried naturally, if care is taken with the design of the fuel storage system.
2. Particle Size
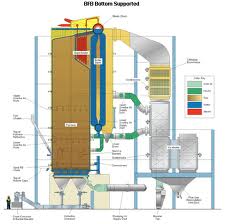
The target biomass particle size is dictated by the type of combustor. Suspension burning requires the fuel to be dried and ground-up or pulverized to a very small size so that it can be blown into the boiler. Most fluidized-bed boilers generally require their fuel to be ground-up to a particle size <63mm (<2 ½”); (see CEN P63 specification). Pin-hole grates or vibrating grates tolerate material <100mm (<4”); (see CEN P100 specification). Both P63 and P100 specifications call for specific size distributions with minimum allowable amounts of acceptable sized material and specific limits of the amounts of both undersize and oversize material. For the best combustor and emissions control operation, the hog fuel particle size being fed to the combustor should be kept within those limits.
Particle size within a biomass pile also has a big effect on moisture absorption, heat build-up, heat dissipation and dry fibre losses. Piles containing a large amount of fines absorb greater amounts of water, generally heat up faster due to greater microbial action, and restrict air movement through the pile, thereby limiting heat dissipation; all of this leading to increased dry fibre loss and possibly spontaneous combustion.
Conversely, piles consisting of large wood chunks heat up more slowly, permit better air flow due to the large voids, dissipate the heat faster due to better air circulation, have lower rates of microbial action and lower dry fibre losses.
It is recommended that for long storage periods that fuel be stored in fairly large particles and only re-processed to the final size shortly before usage in the boiler.
Regular fuel sampling is necessary to ensure the incoming fuel meets contractual requirements and also to ensure that the fuel being fed to the boiler meets the proper size distribution.
3. Contamination
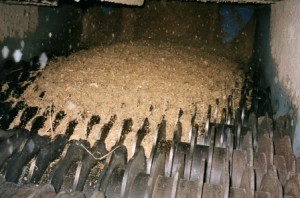
Assume that the incoming raw material will be contaminated with dirt, rocks, grit and metal; and snow and ice in northern climates; the amounts of which should be minimized prior to the fuel being introduced into the combustor. Ferrous metal is relatively easy to remove with self-cleaning magnets, but to be effective, care must be taken with magnet placement.
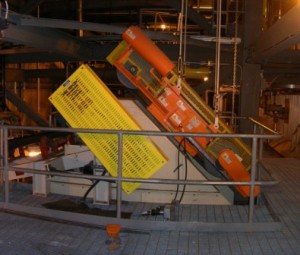
Large rocks and frozen lumps can be removed with disc scalping screens. Dirt, grit, snow, ice, small stones and other such small particles are more difficult to remove. Equipment is available to segregate and remove this material, but it is generally a costly enterprise. It might be best to select a boiler that can handle a certain amount of this material.
However, the best solution is to utilize methods that minimize the amounts of these materials getting into the hog fuel in the first place, including:
- Don’t store processed fuel on un-paved surfaces where they can pick up rocks, dirt and grit.
- Load directly into trucks or storage bins when making the hog fuel.
- Ensure that the contamination that builds-up on delivery trucks does not end up in the hog fuel.
- Store the material under cover whenever possible to minimize the amount of snow accumulation.
Woody biomass can also contain other contaminants that cannot be removed prior to combustion. For example, in coastal British Columbia, Canada, logs are transported by water in log `booms’ along ocean channels and while doing so absorb salt water. Also, bark and wastewood is often transported in open-topped barges where salt-spray splashes over the barge walls. When burned in a boiler, salt can cause problems with the boiler equipment if the proper metallurgy is not used. Also, appropriate emissions control equipment must be utilized that can handle the salt.
4. Calorific, Proximate and Ultimate Values
The most important quality parameter is the calorific value of the fuel; the higher the value the less fuel required, with the converse being true. Also, different fuels will have different proximate and ultimate values. If you utilize a multitude of fuels with very different calorific, proximate and ultimate values, the fuels should be mixed before the boiler in order to have the best steady-state performance of the boiler.
Other Things to Consider
Hog fuel quality depends not only on the raw material characteristics but also on the way that hog fuel is handled. There are several inter-related things to consider when designing a hog fuel storage system, including:
- Type of combustor
- Types of material being stored
- Amount of storage required
- Pile size and shape
- Pile compaction
- Dry fibre loss due to microbial action
- Fire prevention
- Natural air drying
- Climate
- Need to keep fuel dry (or not)
- Dust control
- Tracking the amount of inventory
- Pile building and reclaiming
Type of Combustor
As noted above, the fuel and the type of combustor must be compatible to achieve satisfactory boiler performance.
Types of Material Being Stored
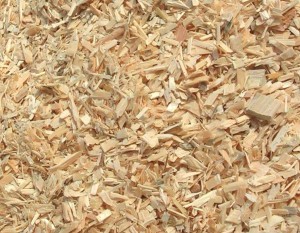
Radically different types of material such as clean wood chips, short rotation coppice (SRC) and forest debris should not be stored in the same pile, as they decompose at different rates, which can lead to spontaneous combustion. They should be stored separately and blended just prior to transport to the boiler.
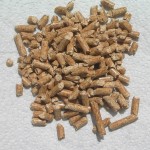
Fuels such as pre-processed wood pellets require special handling. They are uniform in size and moisture content, are very free flowing, but are quite fragile, absorb water and easily degrade. And, the dust created when handling wood pellets is very explosive. Storage in silos is appropriate but care must be taken to accommodate the explosive nature of wood pellet dust.
Amount of Storage Required
The amount of storage required depends upon:
- Minimum fuel storage; how much storage the plant’s financiers, regulators, clients and/or insurers require as a minimum to ensure continuous operation
- Known fuel delivery interruptions; the length of periods when fuel delivery can be anticipated to be interrupted, say for long weekends, or when supplier’s mills are shutdown
- Reliability of fuel delivery; there must be enough fuel on hand to cover likely transportation delays
- Contingency supplies, to cover periods when forests are inaccessible for fire season, the wet season or during spring break-up.
- Fibre supply contractual requirements; the ability to continue to stockpile fuel when the power plant is shut down for annual maintenance.
Often the space available dictates the size and shape of the storage pile and the maximum amount of fuel that can be stored.
Typically, biomass-fired power plants will stockpile a minimum of 20-30 days worth of fuel, but many will store 60-days worth or more.
Pile Size and Shape
The pile storage capacity is a function of the pile size (volume) and the bulk density of the fuel. The bulk density can vary depending upon the size of the particles in the pile, the moisture content and the amount of compaction.
Selecting the correct pile shape is important. Large, high piles have a lower surface to mass ratio, lower heat dissipation rates and tend to heat-up more due to microbial action. Long, low piles have a greater surface to mass ratio, build-up less heat and dissipate heat better. Flat-topped piles absorb rain more readily than do sloped piles which tend to shed the rain. Piles with a lower surface to mass ratio take longer to absorb rain but also take longer to evaporate it.
Pile size has an effect on pile footprint and vice versa. High piles generally have a smaller footprint than do long, low piles of equal capacity. The pile base is usually costly to construct, particularly if paved; so from a cost perspective, a smaller footprint is better. Pile shape is also influenced by the type of reclaim technology selected.
Pile Compaction

Pile compaction varies depending upon the size and depth of the pile, the size of the particles in the pile, and the type of dozer driving over the pile, if any. The larger and deeper the pile, the greater will be the natural compaction. The density near the pile edges will be significantly less than near the middle. And, because of their smaller tire footprint, rubber-tired vehicles compact biomass more than do tracked vehicles.
Smaller particles compact differently than do larger particles, so particle segregation within a pile will result in different densities. Particle size segregation naturally occurs as a pile is being built; larger particles tend to roll down the surface to the outer edges of the pile. Additionally, size segregation is greatly affected by wind, which will concentrate fine particles in one or more parts of the pile.
Some compaction studies have shown that the density deep inside a large pile can increase by 25-30% higher than the surface density and the overall pile density can increase by 14-15%.
Dry Fibre Loss
Microbial biological action within a biomass pile results in fibre losses. Some studies show that more than 1% of useful fibre can be lost per month of storage due to biological action. Consequently, the plant must bring in more material to make up for this loss, which can involve substantial additional costs.
Biological action is affected by the type and species of biomass being handled, moisture content, temperature, and the amount of oxygen present. With sufficient oxygen, microbial action will increase as the moisture content and temperature increase.
Some studies show that the losses due to biological action are lower in highly compacted piles where the amount of oxygen is restricted.
Other studies have shown that if air flow is enhanced, the heat can be dissipated and biological action slowed down, thereby reducing the amount of heat generated.
Other studies have shown that microbial action is most active and resulting fibre losses the greatest, within the first week of storage. Consequently, some believe that when fresh hog fuel is being delivered, that hog fuel storage piles should be operated on a last-in, first-out (LIFO) basis, so that new fibre is used immediately when it is first brought in (`hot’ feed to the boiler), before microbial action can occur, thereby minimizing the dry fibre losses. However, when reclaiming from the long-term storage pile, reclaiming should be done on a first-in, first-out basis (FIFO) in order to use the oldest fuel first.
Dry fibre loss can be further minimized by the following practices:
- For long-term biomass storage, store the material in as large particles as possible, with a minimum amount of small particles which can fill the voids and restrict air flow. This practice will necessitate re-processing the hog fuel into particle sizes acceptable to the boiler shortly before the fuel is conveyed to the boiler.
- Do not compact the storage piles, thereby enhancing natural air flow through the pile and assisting heat dissipation and decreasing biological action.
As a side effect of dry fibre loss, the ash content rises when expressed as a percentage of the dry fibre left, as the amount of non-organic material in the fuel is not affected by microbial action. Therefore, the higher the dry fibre losses, the higher the ash content in the fuel delivered to the boiler.
Fire Prevention
Heat can build-up within hog fuel storage piles to the point of spontaneous-combustion, which can result in huge inventory losses and potential damage to structures and equipment.
Fires will smoulder deep inside a pile for a long time. When a pile is opened up and exposed to oxygen, the fire will flare up into open flames. About the only way to extinguish a hog fuel pile fire is to open the pile, spread it out on the ground and extinguish it with lots of water. High, large volume piles on small footprints are harder to take apart than are low spread-out piles.
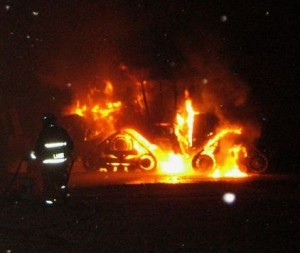
Mills and power plants with biomass storage piles have learned the hard way to minimize pile sizes in order to minimize the hazard and losses associated with fires in large piles and will often employ multiple piles separated by fire breaks.
Dust will build-up on any flat surface. Some of the worst fires are started as a combination of fine dust and hydraulic oil and snow packed around heat generating equipment.
If piles are dressed with mobile equipment, care must be taken to ensure fires are not started by dust building-up and igniting around hot exhaust systems.
All structures and equipment should be equipped with spark and fire detection and suppression equipment. In extreme cold climates, multiple zone, dry sprinkler systems should be used to minimize the wetted areas and consequent freezing when the system is tripped.
Wood pellet dust is highly explosive as well as being inflammable; so explosion detection and suppression systems must be used.
Natural Air-Drying
Natural drying can occur as a result of the internal heat from microbial action and good airflow through the pile; more so than from the effect of climate. Building the pile to enhance natural air flow through the storage pile increases the drying effect.
Studies have shown that it is possible to drop the moisture content of hog fuel from 45% MC to 30% by natural air flow means only; but depending upon the climate, it will require a time period of 30 – 60 days.
Care must be taken not to mix forest residue, SRC and clean wood chips in one pile; the different rates of microbial action will cause uneven heating and drying.
Pile size and shape has an effect on natural drying. Piles with a large volume to surface area ratio generate more heat, have lower air flow through the pile and dissipate heat slower and therefore dry slower.
Conversely, outdoor piles with a high surface area to volume ratio have larger surface areas through which they can absorb more rainfall and therefore can be in an on-going wet-dry-wet cycle; this is a big factor in very wet climates.
Piles subject to high rainfall can have an insulating wet layer between 1.0 – 3.0 m deep, which impedes air flow, increases the internal temperature and reduces heat dissipation leading to greater microbial action, more heat build-up and possibly spontaneous combustion. A snow cap on top of the pile can have the same effects.
Piles containing a lot of fine material have higher rates of microbial action and heat build-up, absorb rain easier and have lower air flow rates and therefore dry slower, if at all.
Compacted piles have lower air flows and dry slower.
The Need to Keep Fuel Dry (Or Not)
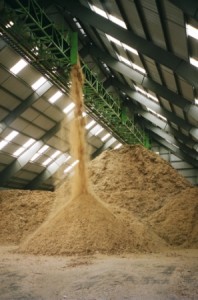
The advantages of keeping fuel dry are numerous and seem to make sense, but imply that the pile will be covered to protect it from the weather. However, the choice to keep fuel dry is not so simple, particularly if large volumes of material are involved. For example, a 30 MW biomass-fired power plant requires >600 BDt/d of fuel occupying 3,585 m³/d loose volume. Therefore, 20-days usage will require approximately 71,000 m³ of storage. This will be equivalent to a 21 m high longitudinal, conical pile with a footprint of 42 m x 90 m. To cover this would require an A-frame building 33 m high with a footprint of approximately 54 m x 115 m, including room for stacking and reclaiming equipment. A building this size is very costly.
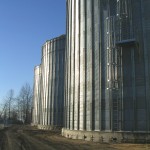
Some fuels, such as wood pellets, which absorb water easily, must be kept dry. Fortunately wood pellets have great flow characteristics and are very suitable for storage in silos.
In addition to keeping fuel dry, there are environmental and aesthetic reasons for covering your biomass fuel piles, including:
- Minimizing fugitive dusting if in or near an environmental or residential sensitive area
- Hiding the piles from view if in a town or city
Climate
Climate has a big influence on biomass pile storage. Special measures are required for extreme climates with high rainfalls, large snowfalls, high winds, very hot or extremely cold temperatures. Some climates can also help to dry biomass, if the piles are constructed as described above.
Dust control
Dry biomass can be very dusty. Fugitive dust will escape at every process or handling point if measures to contain it are not provided for. There are (4) main parts to good dust control:
1 Minimizing dust generation
- Store biomass in as large particles as possible, as long as possible
- Minimize drop heights of processed fuel
- Minimize conveyor speeds
- Use low speed shredders
2 Dust containment measures including:
- Enclosing all processing equipment and transfer points
- Maintaining negative pressures inside enclosures and structures
- Protecting conveyors from wind
- Erecting wind fences to protect open piles from winds
3 Dust collection
- Connect negative pressure dust collection systems to all enclosures to minimize fugitive dusting and collect the airborne dust
- Discharge the collected dust into sealed containers and dispose the dust appropriately
- One thing that might be considered with covered storage buildings is drawing the boiler combustion air from the building to keep the storage building under a negative pressure and thereby minimize fugitive dusting. This also helps to minimize the problems of off-gassing and odour control, which are associated with biomass storage systems.
4 Clean-up Program
- No dust control system is perfect and dust will build-up if left in place long enough, so institute a clean-up program.
- Utilize a vacuum system to clean-up spills and dust build-ups.
- Do not use air to blow dust away as it will just spread the airborne dust, which can be quite explosive. Also, the blown dust will just settle out elsewhere.
Tracking the Amount of Biomass Inventory
Where any bulk, raw resource is used in an industrial process, there is a requirement to track both usage and inventory. And with the increased movement to utilizing biomass as a fuel source, more companies are discovering the difficulty in accurately measuring biomass inventory. This problem should be considered during the design of the pile building and reclaiming systems.
Accurately determining the amount of fibre in biomass piles has long been problematic and even today with accurate measuring devices, fibre pile measurement doesn’t have an easy solution. Pulp and paper mills everywhere have struggled with this problem for years. One year they will have to write-off costly wood chip inventory that appears to have disappeared; the next year they will have too much inventory. Other facilities that utilize biomass have similar inventory assessment problems.
The problems stem from the variability of the basic physical properties of biomass, including, different species, moisture content, different basic and bulk densities, varying amounts of compaction and dry fibre loss. Additionally, using multiple inventory tracking measures, including `green’ or bone dry tonnes (BDt), solid wood or bulk densities, and solid wood volumes or bulk volumes, lead to inventory errors when converting from one measure to another and back again.
Following are some suggestions for accurately tracking inventory.
- Ensure frequent pile turn-over, to minimize losses due to biological action or spontaneous combustion.
- If space is available, use a multiple pile system where piles are routinely `zeroed-out’, or emptied completely; this way the inventory can be rationalized more frequently so that errors don’t accumulate.
- Do not rely on `rule of thumb’ conversion factors to convert between volume, wet weight and mass; and do not track biomass inventory on a volumetric (m³) or green weight (Gt) basis, as neither reflect the true amount of dry fibre present. Track the tonnage in BDt rather than in Gt or in m³.
- Rely on accurate measuring of the flows into and out of the chip pile. Utilize multiple, redundant scales on both the infeed and outfeed from a pile, so that a malfunctioning scale can be quickly identified; and, recalibrate the scales at least twice per year, summer and winter.
- Measure the ever-changing moisture content (MC) of both the incoming and outgoing biomass so that the true amount of dry fibre (BDt) can be accurately calculated from the Gt scale measurements.
- Moisture content can be measured by on-line moisture sensors or by lab analysis of biomass samples from both incoming and outgoing flows.
- The true amount of fibre remaining in a pile (BDt) at any one time would be the difference between the incoming and outgoing amounts.
Note: Tracking the amount of biomass inventory is covered in more detail in another article titled “Chip / Biomass Pile Inventory Measurement”, which can be seen on my website.
Pile Building and Reclaiming
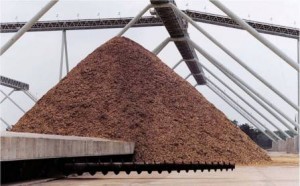
There are many different methods and types of equipment for pile building and reclaiming. Each has its advantages and disadvantages. Pile building and reclaiming systems range from the fully manual to fully automatic. Equipment choice should consider the type of fuel being handled, the fuel requirements of the boiler and the possible requirement for redundancy. This is a big topic, which I will write about in another article sometime in the future.
It is my experience that in order to minimize operating costs, inexperienced entrepreneurs embarking on biomass-fired power plant projects want to have fully automatic systems with 100% live-storage. If they are also planning on storing large volumes of fuel, 100% live-storage can be prohibitively costly.
Generally, once an order of magnitude capital cost has been prepared and the client sees what the capital cost is going to be, pile sizes are reduced and the requirement for 100% live-storage is dropped. So, it is a good idea to prepare a feasibility study before embarking on process definition or detail design.
Conclusions
As you can see from the foregoing, there are a lot of factors to consider when designing a biomass storage system. Almost assuredly, the factors that dominate the design at one facility will not apply at another similar plant. It is strongly recommended that you employ a biomass handling specialist with lots of experience to assist you in designing the most appropriate system for the material being handled that can be accommodated on the site and that will fit your budget.
Usually if during the early design phases, proper consideration is given to the fuel quality, storage and reclaiming requirements, the resulting fuel handling system ends up being a technically simple process. However, all of the factors described in this document need to be considered when designing a biomass storage system.
Because of all of the physical variables of fuel types and sources and the possible combinations with the end uses to which the biomass is being put, and environmental, commercial and contractual items to be considered, it is not possible to make firm recommendations that cover all biomass storage installations. However, it is possible to make a few generalizations, including:
- Ensure the moisture content of the fuel being delivered to the boiler is within the design limits for the boiler.
- Store the biomass in as large particles as possible and do the final size reduction shortly before the biomass is conveyed to the boiler.
- Remove as much of the contaminants as is technically or economically feasible.
- Consider the fuel requirements of the combustor.
- Store radically different materials separately and blend to obtain a uniform product after storage and prior to being conveyed to the boiler.
- Don’t store more than is necessary to efficiently operate the plant without causing downtime due to fuel shortages.
- Determine the optimum pile size and shape for the specific biomass being handled that best meets the requirements of the process and fits the site.
- Don’t compact the piles by driving on them with mobile equipment.
- Design the system to minimize dry fibre losses due to biological action or spontaneous combustion.
- Provide for dust control, and spark, fire, and explosion detection and suppression systems as required.
- If space allows, utilize multiple piles separated by fire breaks.
- If you have wet fuel, design the storage system to take advantage of natural air-drying.
- Institute an accurate fibre tracking system.
- Determine whether FIFO or LIFO is appropriate for your process.
- Select reclaiming equipment that is appropriate for the material being handled.
Glossary
BDt bone dry tonnes
CEN European Committee for Standardization
d day
FIFO first-in, first-out
Gt green [wet] tonne
LIFO last-in, first-out
m meter
m³ cubic meter
mm millimetre
MC moisture content
MW megawatt
SRC short rotation coppice
About the Author
Paul Janzé has more than 30 years experience in engineering design, project management, equipment manufacturing and maintenance, primarily in the forest products and energy industries. His biomass handling and processing experience includes forest residuals, logs, lumber, chips, bark, woodwaste, pellets, straw and poultry litter, animal tissue, sludge and biosolids. Additionally, he has experience with other industrial materials municipal solid waste (MSW), lime dust, coal and ash handling.
He has a keen interest in technologies which recover and utilize waste materials and convert them into products such as wood pellets. Paul’s specialties are fibre flow analysis and mass balances, conceptual design, process optimization and designing novel solutions to complex processing and handling problems.
Dear Paul,
I totally agreed with you on what you have explain in your article on biomass storage pile basics. At the end of the day, the success of the biomass storage system would be a system that works well for the project at a reasonable cost. Still it is rather complicated as no 2 projects are the same.
The receiving and processing is more straightforward. The covered storage and retrieving is more complicated especially when the amount to be stored is 60,000 tons to 120,000 tons.
Regards,
John Pong
Great document on storage of biomass fuel. Curious… Who can I talk to in reference to the assessment of a Hog Fuel storage problem in a remote are of North West BC. I need to get an idea of costs to remove, repair, or replace a current combusted hog fuel outdoor storage area that has been blowing progressively more and larger blue plumes of smoke that are contributing to air borne health issues. Need this assessment for documentation to provide to current owners of this hog fuel. Your expeditious response appreciated.
thanks!
Hello Julie,
Thanks for visiting my website.
Putting out fires in hog fuel piles is not easy. About the only way to extinguish a fire that is smouldering deep inside a pile is to dig into the pile, spread the burning material on the ground and hose it down. It sounds easy but it isn’t necessarily so. Extinguishing these fires can be a long, tedious and dangerous process, depending upon the size of the pile and the extent of the fire hidden inside.
There are several things to consider:
– Do not rely on cold weather to kill the fire. There are many instances of hog fuel piles burning at very cold temperatures <-20°C. - Do not venture on top of the pile as the fire could burn-out a hollow inside that you can't see and which could collapse underneath you. - Soaking the pile with water will not be effective as the water will penetrate only a few meters and then it will form a wet `cap' of material that will shed the water and will seal the heat inside the pile; thereby compounding the problem - Consult with the pertinent authorities before attempting to extinguish the fire. i.e. - the local fire marshall or the local forest service representative, who will likely help you develop an appropriate plan. - As soon as the smouldering material is exposed to air it will flare-up into open flames. - Have lot's of water available. - Establish a safe work procedure and have lot's of back-up available. - Use appropriate personal protective equipment (PPE). - Try to collect and treat the leachate from the fire extinguishing process. Unfortunately, I do not know of any company that specializes in extinguishing these fires; but, I would imagine that either or both the local fire marshal or the forest service would have an interest in seeing the fire extinguished, as the fire could easily flare-up and spread either to an occupied area or to the forest. I am sure that the owner has the responsibility to extinguish the fire and must do so if ordered to by either the local fire marshal or the forest service, no matter the cost. How big is the hog fuel pile? Where is it located? I see that you are a doctor and as you are concerned with health issues I am assuming that you are a doctor of medicine. Am I correct? Surely, the local health board will have concerns about the air quality and would give you support. Another resource that you could call on would be the ministry of the environment who has strict air emission guidelines. If it is near an operating plant, the ministry of labour would likely be interested as well. Please keep me posted on the status of this burning hog fuel pile. I'm sure that there are others who would be interested in following the story, too. Paul
Hi John,
Thanks for visiting my website. Handling, processing and storing biomass has been done for centuries; but it is only the last few years that there has been a concern for doing it properly, both for the business involved and for the sake of the environment. The greatest thing about biomass is that it is a renewable resource, but that doesn’t mean that the forests and their products are unlimited and that we can treat them with disregard. The recent focus on biomass as a `green’ source of fuel for energy is threatening to put extreme pressure on all forms of biomass, not only the forests. We should use this valuable resource, but we should not over-use it or abuse it. If we take care of it, it will be with us forever. If we don’t take care of it, we won’t be around to see the effects.
I see that you are a representative for Elgrey Power in Singapore. What can you tell me about your company? I work for a large engineering company, who has specialized in designing and constructing biomass handling and processing systems and biomass fired power plants for decades and would be interested in learning more about your company and projects.
Paul
I have some concern regarding pile shape. I understand your description that the hog fuel “knits” and is not very fluid; however, with high almost vertical walls does the pile risk collapse as would occur with soils? Has a soils engineer provided an assesment of this material?
Otherwise, I found your article to be very helpful in our management of the fuel piles.
Hi Jim,
Thank you for visiting my website. After consolidation in a storage pile, hog fuel will form near-vertical walls when a dozer cuts into the pile. And yes, the walls eventually do collapse’ but the dozer operator needs to be very careful that he doesn’t get buried when digging away at the pile. Of greater danger is a hog fuel wall collapsing when the dozer is on top of the pile near the edge.
Hog fuel characteristics can vary widely from free-flowing, dry sawdust to wet, stringy bark and any combination between. In today’s market where there is not a lot of spare fuel to be had, most plants take what they can get. Consequently, hog fuel characteristics can vary significantly over short periods of time. I don’t know of any soil engineer’s report on hog fuel; and any report would only be specific to the exact material being tested. It could change tomorrow.
However, when designing a biomass fired power plant, it is essential to know the characteristics of the proposed fuel, including: material constituents, species, moisture content, basic wood density, bulk density, material size distribution, calorific value, ash content, chemical make-up, contaminants, etc.
What are the circumstances that prompted your query?
Paul
Do you consult for individual companies if so can you E mail me contact info
Great article! Can’t wait to read your article about Pile Building and Reclaiming. Will you also cover the effects of piles shapes and sizes more detailed?
Sandra
Do you think it is safe to have one person on site at night with a very large hug fuel pile? We’re talking 40 feet high and 10 times as wide? There are three people on call if a fire happened, but i wonder if there needs to be at least two people present….I guess that the one guy could just stay by the phone and wait for help to arrive–10- 15 minutes…by then i wonder if the fire would be impossible to extinguish?
Hi Gerry,
The long answer:
Three things must be present for combustion to occur: a fuel, oxygen and an ignition source. Most fires in long-term, hog fuel storage piles happen as a result of spontaneous combustion. By the time a hog fuel fire flares up into open flames, it will likely have been burning inside for quite a long time, and you should have seen evidence of that from either excessive amounts of steam from moisture being evaporated or from smoke being emitted from the pile. The flare-up happens when fire burns through the surface or the pile is opened up during normal reclaim operations and the hot spot is exposed to a ready oxygen source. Wetting the surface of the pile will only extinguish the top meter or so. Extinguishing a fire inside such a large hog fuel pile is risky as you don’t know how far it has burned inside the pile until you open it up, and opening it up is dangerous. You will most likely need heavy equipment and a large crew. On very large, out-of-control, open hog fuel pile fires, I have heard of aerial water bombers being employed to extinguish surface flames and prevent fire from spreading; but in the end, the piles have to be opened up bit by bit and each section extinguished.
It is far better to expect that fires will occur in long-term hog fuel storage piles and take early steps to control them.
– Have an underground fire header ring with hydrants spaced evenly around the pile.
– Don’t store wet and dry material together in the same pile.
– If you have room, store the material in several smaller piles with adequate fire breaks between them. Also, smaller piles have a greater surface to volume ratio and depending upon the average particle size and amount of compaction could promote better air flow, hence cooling and drying.
– Don’t create piles higher than you can reach from the ground with the equipment available. You don’t want to be driving a dozer on top of a burning pile.
– Set up a periodic temperature monitoring procedure, either by digging test holes into the pile or using long temperature probes.
If you are worried about an external ignition source setting fire to a hog fuel pile, there are things that you can do to mitigate the risk.
– Build your pile a long way away from known ignition sources such as beehive or olivine burners.
– Ensure that all mobile equipment operating on or around the pile are in good maintenance, are cleaned at least once per shift and are fitted with automatic extinguishers.
– Keep all dry brush cut back a long distance from the pile.
– Institute and enforce a strict no-smoking policy.
– In extremely dry conditions, wet the surface of the pile.
The short answer to your query:
I suggest that you engage with your local fire chief and get his input and support; he is the expert.
Paul
As a northern pulp mill – as with all pulp mills – our biomass needs to remain plastic free due to our inability to remove the plastic once it enters our digesting process in the kraft pulping process. Curious if there are best practices / containment systems from the dumpers, conveyors, to entrance in digester? Frustrating and expensive issue.
Hi Amber,
Thank you for visiting my website.
First, I would like to say that I work for Ausenco (formerly Sandwell Engineering) in Vancouver, BC as Manager, Wood & Biomass Handling and I know the DMI Kraft pulpmill and personnel in Peace River, AB well, having done many projects there over the past 25 years. Most recently in 2014, we did the conceptual and detail design for the combined chip truck / railcar dumper, which as you know was unfortunately cancelled at the last minute.
Indeed, plastic contamination in pulp is a small but significant problem in pulp manufacture; the amount of plastic in one small plastic pen can ruin 1000 tonnes of pulp. Generally, the industry has done a great job of controlling the amount of plastic used in a pulp mill, and DMI is one of the best.
Unfortunately, there is no `magic bullet’, when it comes to eliminating plastic contamination. It takes rigorous attention to the following steps, and even these do not guarantee complete elimination. The well-known key steps in minimizing plastic contamination are:
1. Keeping tramp plastic out of the wood chip supply stream into the mill is the best way to reduce plastic contamination. This requires working with your wood chip suppliers and haulers to educate them about the consequences of plastic contamination and ensuring they are taking the necessary steps to keep tramp plastic out of the chips. It is also a good idea to conduct unannounced audits of the wood supplier’s facilities.
2. Instituting a good `plastic is drastic’ awareness program in the mill, and training everyone to be on the lookout for and picking-up tramp plastic and disposing of it properly.
3. Minimizing the use of plastic in the mill, particularly where it has a chance of getting into the fibre supply.
4. Using `pulp-safe’ plastics where plastics are required.
• Generally, pulp-safe plastic is considered to have a melting point >160°C and a specific gravity >1.0.
• Redwood Plastics makes a wonderful pulp-safe UHMW wearplate called `Synsteel’, that has good, low-friction anti-wear characteristics and has metal embedded in it that enables the material to be picked-up by a magnet or detected by a metal detector. DMI uses Synsteel almost exclusively for wearplates.
• Redwood also makes another plastic wearplate called SPS, that dissolves in the Kraft pulping chemicals.
Unfortunately, most tramp plastic has similar physical characteristics to wood in that it is light and buoyant, so cannot be separated from wood by air density separation or flotation.
Optical sorters are used in material recovery facilities (MRF’s) for separating plastic from other materials and can even separate different types of plastic. Optical sorters do a reasonable job of sorting plastic where a large percentage of the material flow contains plastic, but they are not 100% effective and are almost always followed-up by a sorting belt where humans pick through the remaining trash looking for plastic. Optical sorters would not be effective in keeping plastic out of chips or pulp, as the amount of plastic that can cause damage is so infinitesimal, in the order of -1×10 (to the 9th power) by weight. Even detecting that small amount of plastic in the chip flow is near-impossible.
DMI already has a good plastic awareness program, but if there is a high-turnover of mill personnel, it might be necessary to `step-up’ the program intensity.
Once tramp plastic lands in the truck dumper receiving hopper and makes it onto the chip pile, it is nearly impossible to detect and remove, unless it is a large piece of coloured plastic that the chip dozer operator can see.
I suspect that most plastic contamination at DMI is tramp plastic that comes from outside the mill. The likelihood of this source becoming worse is greater if you have a lot of chip suppliers or a lot of new chip truck drivers. So, that means working with the chip suppliers and haulers and making them aware of the dangers of plastic contamination. Penalizing chip suppliers or haulers doesn’t work, because it can be months between the original `plastic-in-the-chips’ contamination and the `plastic-in-the-pulp’ contamination, so you can’t actually determine where the plastic originated.
I know that I haven’t offered any new information, but that is the state of the situation as I believe it to be in the industry.
The next time I am at the mill, I will look you up.
Paul
Hello Paul
I have enjoyed reading your materails and you have shed light on several topics that did not make sense to me previously.
I work in Indonesia and have recently been given the responsibility for fire protection at a large chip mill. One of my challenges is a large biomass pile about 300 m x 300m by 50m in height that has been produced after several years of wood chip production .
Since my arrival a couple of weeks ago I have noticed that there is ongoing spontaneous combustion in the pile. The fires are dug up and sprayed down with large amount of water only to come up again the next day in a different place.There are no boilers on site and there is no appetite to use the biomass for anything . The bio mass is made of acacia bark in various stages of decomposition, a fair amount of timber shorts and mature compost in the mix. The resident engineers are considering covering the whole thing up with soil or concrete . There is so much variability in the material that I doubt that we will ever get any stability in the pile to close it up correctly. I also think that it’s just going to keep burning for a long time and eventually collapse in places.
What are your thoughts? Do you have any ideas that we could consider? Thank you for your time.
Hi Fred,
Following are my comments and recommendations.
DEALING WITH A WASTEWOOD PILE FIRE
Caution
Fighting fires is always a risky task, so:
1. Do not walk on or drive on top of a pile suspected of having fire burning underneath; the fire may have burned a hollow inside and the pile above it could collapse.
2. Do not dig from the top of the pile, as a smoldering fire will flare-up when exposed to air.
3. Use appropriate PPE and firefighting gear.
Strategies That Don’t Work
1. Soaking the top of the pile will only saturate the top 1-2m of material and then the water will simply run off. Water will extinguish a surface fire but will not penetrate into the interior of pile to extinguish a fire deep inside.
2. Trying to soak a pile with water results in a considerable amount of run-off leachate and contaminated water that must be dealt with.
3. Burying the pile with dirt, sand or concrete in an attempt to smother the fire, will not work. Even starved of oxygen, the fire will get enough air that it will continue to smolder for years.
4. Don’t add fresh material on top. You are literally adding fuel to the fire.
Extinguishing A Wastewood Pile Fire
The only way to extinguish a fire in a large wastewood pile is to:
1. Dismantle the pile. Dig into the pile from the side of the pile to expose the burning embers, but be careful because they will flare-up when exposed to air.
2. Spread the burning material out on the ground and extinguish the fire with fine water sprays.
3. Utilize a trommel screen to reclaim the large, usable material (if any).
4. Dispose of the burned material in an environmentally safe manner.
Comments
1. As long as wastewood is stored in such a long-term pile, expect that spontaneous combustion will occur due to biological action and oxidation. It’s going to happen, so avoid long-term storage.
2. There is a well-known peat bog here in BC that has been burning underground for over a hundred years and maybe longer. Every summer when the water table drops, the fire flares up above-ground and they use water bombers to extinguish the above-ground fire, but the peat continues to burn underground.
3. I know of one 50-year old wastewood pile at a pulp mill that has been smoldering for decades, and the owners have been trying to extinguish it for decades. Over the years they buried the pile with sand in an attempt to smother fires. Now they want to reclaim the good material from the pile and are having to deal not only with still-burning material, but also heavily contaminated material.
4. Some mills have realized that fires in old biomass piles cannot be extinguished once and for all time unless they dismantle the entire pile, which they will do if the burning pile threatens people, structures or valuable raw material. However, if a smoldering pile is not a threat, some mills have adopted a `live-with-it’ attitude, monitoring the pile constantly and extinguishing the surface fires when they flare-up.
Did you read the article titled “Biomass Dust Fire and Explosion Control” on my website? It contains some useful information.
So, no `magic bullet’ solution, but I hope that this is of some help.
Paul
hello, or mill has a big hog pile , smoking all the time , we have started feeding into our bee hive burner which we just fired up to get rid of our hog pile. the problem we are having as this hog just won’t burn hot enough or fast enough to get the hog piled cleaned up in our 9 month window that we have a permit for to burn this shit. Any ideas on how to get this hog to burn or other alternatives would be greatly appreciated … or steer me in the right direction for some advice.. do we need more air or??
Hi John,
Thanks for visiting my website. I see that you work for Tolko. Just curious, but is this at the old OSB mill in Slave Lake, AB?
This is a tough one. I think that practical options are quite limited, as this is a one-off situation where you don’t want to spend more than necessary to get rid of the hog.
How much material do you have to get rid of? If the hog won’t burn, it must be quite wet; do you know what the moisture content is?
Is your burner the Olivine type with combustion air fans? As you suggest, more air injected under the pile in the burner should help. Also, do you have any drier material that you can mix with the old hog? Does your permit allow you to temporarily burn old tires or railroad ties?
Can you retrofit the burner with a natural gas burner to help drying and combustion?
Is the hog contaminated with a lot of sand and dirt, which holds water? If the sand and dirt content is high, you might consider running it through a trommel screen to remove the dirt laden fines <1/4”, which BTW make a good soil amendment material.
One thing that might help down the road is to start turning the material over and spreading the hog out, if you have the room. Perhaps it might air-dry a bit before you burn it in 3-4 months.
Can you split the pile up into smaller piles and open-air burn them all simultaneously? They may burn slowly, but if you have enough of them burning, the hog should be gone within your 9-month timeframe.
I hope this helps. Let me know how it all works out.
Paul
Dear Paul,
My woodchips are too wet & clogged up my hopper, it can’t seem to go down. What solution do you have? Please share with me based on your experience.
I have the video to show you. Please let me know how to send it to you.
Thank you.
Dear Paul,
Over the course of a period of time, say six months, how much will typical Southern pine bark degrade with regards to the HHV? I’ve tried to find this data, but I haven’t had any luck thus far.
Thanks,
Philip
Hello,
I’m the Ops manager at Whitecourt Power in Northern Alberta. We have had pile fires in the past and as you have mentioned they are very difficult to extinguish. My question is about early detection of a fire or excessive pile heating. Do you know of any methods that work well? I have heard that Temperature probes inserted in the base of the pile or a thermal camera to scan the external of the pile for hot spots may wiork with varying success. If you know about the temperature probes I would like to contact the supplier or the companies using them.
Regards,
Brennan Anderson
Re: Whitecourt Power
Hi Brennan,
Thank you for visiting my website, http://www.advancedbiomass.com . This is a tough challenge that to my knowledge no one has successfully accomplished. Early detection of pile heating is theoretically possible and there is equipment available that could do it. However, the challenge is in implementing temperature monitoring in a practical and cost effective manner.
Your goal is to minimize fires, so if you are going to monitor temperature, you should also be measuring moisture content; both of which can be contained within the same instrument.
A lot of companies make temperature / moisture measuring instruments for biomass, but the longest probes I’ve been able to find are only 1.5m long, which would not be of much use in a wastewood / hog fuel pile that is 15-20m deep. Likewise, I believe that thermal imaging cameras are effective for only the temperatures at or near the surface of a pile.
The presence of CO, CO2 or CH4 can be indicative of a fire, but monitoring those gasses in an outdoor pile is impossible.
Long temperature / moisture sensing cables are used in biomass storage silos, but would be vulnerable in an outdoor storage pile with mobile equipment running about. However, if you are planning on storing biomass for a long period of time in a static pile with no mobile equipment, one alternative would be to push multiple perforated 3” pipes down into the pile, periodically spaced, after the pile is built and hang temperature sensing cables inside. Then before reclaiming the pile, remove the cables and pipes. I believe that wireless sensing models are available, which would eliminate excessive amounts of wiring. I don’t know of anyone doing this, but if you try this, let me know how it works.
Monitoring temperature and moisture is just the first step. You need a plan for when the temperature goes too high; i.e. – what do you do then?
Changing your pile management procedures might be a less costly solution to the problem. If you have the space available, it might be better to store the biomass in smaller piles which permits pile turn-over, where you are always using the oldest material before it has time to heat and self-combust. And, smaller piles have a greater surface area-to-mass ratio and dissipate heat better.
Also, if a fire does occur, being in a small pile it is isolated from the rest of the material and you have better access to it for material removal and fire-fighting purposes.
Paul Janze
Advanced Biomass Consulting Inc.
Langley, BC, Canada
tel: 1-604-505-5857
pjanze@telus.net
http://www.advancedbiomass.com