Introduction
Most raw materials for plants that process woody biomass are delivered in bulk trucks and some are delivered by railcar. This article concerns biomass delivery by truck and the systems available for unloading the trucks.
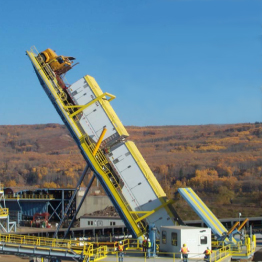
Residual chips, shavings, and sawdust from sawmills are delivered primarily by truck to pulpmills, pellet plants, and panelboard plants. Woodwaste (hog fuel) from sawmills and other raw log processors is delivered by truck to biomass-fired energy systems and cogeneration plants. Wood pellets are delivered by truck and by railcar and are loaded onto ships or delivered direct to biomass-fired power plants.
Delivery by Truck
There are many different types and sizes of trucks used depending upon the material being handled, the weather conditions, the unloading facilities available, distances traveled, the types of truck available, road conditions, the most economical transport method, road weight allowances, required throughput capacity, etc. There are generally two types of trucks used: self unloading and non-self unloading trucks. Continue reading →